Compulsory mixers M / MH Serie are suitable for the mixing of refractory concrete mixes that are designed for firebrick linings, for instance, in foundry furnaces, blast furnaces, heating plant boilers, coke-oven batteries and chimneys in the metallurgical and chemical industries. Compulsory mixers are also used to mix a wide range of construction materials in the construction industry, namely plastering, grout, and repair mixtures. Compulsory mixers are also suitable for the industrial mixing of mixtures during which material is processed by individual batches.
ADVANTAGES
- perfect mixing of individual components over a very short period of time
- variability of stirrers enables mixing of various types of mixture
- a soft starter facilitates a continuous blade startup (with models with an output exceeding 5.5 kW)
- special construction of the cover prevents mixture spillage
- mixing arms can be equipped with spatulas preventing damage and fast wear and tear
- use of enhanced safety features (no-voltage trigger, terminal switch)
- minimal maintenance operation
- rugged construction enabling work in demanding conditions
- low operational and maintenance costs
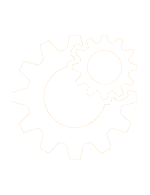
Working principle
Compulsory mixers work on the principle of mixing arms that rotate at a very high speed around the inner axis of the static mixing tank. Mixing is done by several arms which ensure that the mixture is wiped off the sides and the bottom of the mixing tank. The mixing arms can be adjusted sideways and in height and they can be equipped with spatulas.
Depending on the type of mixed compound, mixers can be fitted with several kinds of stirrers
The mixer models designed for the mixing of abrasive materials have their mixing drum provided – up to their utility mixing height – with a replaceable lining made of standard or abrasion-proof material. Alternatively, the mixing drum itself can be made of abrasion-proof material.They are offered two basic mixer types, each characterized with a different construction:
- Standard construction with wheels
- Heavy-duty construction (MH Series)
The mixture is filled via a screen on the cover of the mixer. The screen is equipped with a separating comb for bagged mixtures. The construction of the cover prevents any spillage of material over the sides of the tank. If need be, the mixer can be provided with covering sheet metal to prevent the leak of thinner or dusty mixtures. The prepared material is released by turning the movable segment on the bottom of the tank.
The mixing tank is firmly connected to the stand that can be equipped – in the case of models M 50 – M 250 – with wheels. The M 50 – M 180 mixer models are fitted with height-adjustable posts allowing for the variable height of discharge.
The drive of the mixing arms is ensured by a low-maintenance, worm, or front-cone electric gear unit. The smallest types of mixers (M 50/230V, M 50/400V, and M 80/230V) are fitted with a maintenance-free electric gear unit. Models with a motor output of 5.5 kW and higher are equipped with a soft starter that facilitates a continuous blade startup.
To ensure maximum safety of the service personnel, enhanced safety features have been employed such as the no-voltage trigger and a terminal switch switching off the engine when the cover of the mixer is opened.
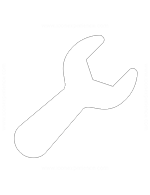
Technical data
Parameter | M 50 | M 80 | M 125 | M 180 | M 250 |
Volume of the tank [l] | 74 | 111 | 162 | 233 | 330 |
Max. usable volume [l] | 37 | 69 | 102 | 148 | 208 |
El. motor output [kW] | 1,5 / 2,2 | 2,2 / 3,0 | 2,2 / 3 / 4 | 2,2 / 3 / 4 | 4 / 5,5 |
Voltage [V] | 230 / 400 | 230 / 400 | 400 | 400 | 400 |
Rotation of the mixer [rpm] | 47 | 47 | 47 | 47 | 47 |
Max. grain size [mm] | 10 | 10 | 16 | 16 | 20 |
Weight [kg] | 96 | 131 / 137 | 147/177/187 | 172/202/212 | 270/390 |

Photogallery
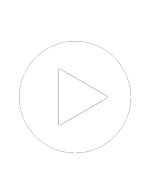
Practical demonstration
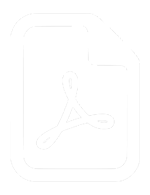
Download
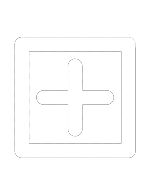